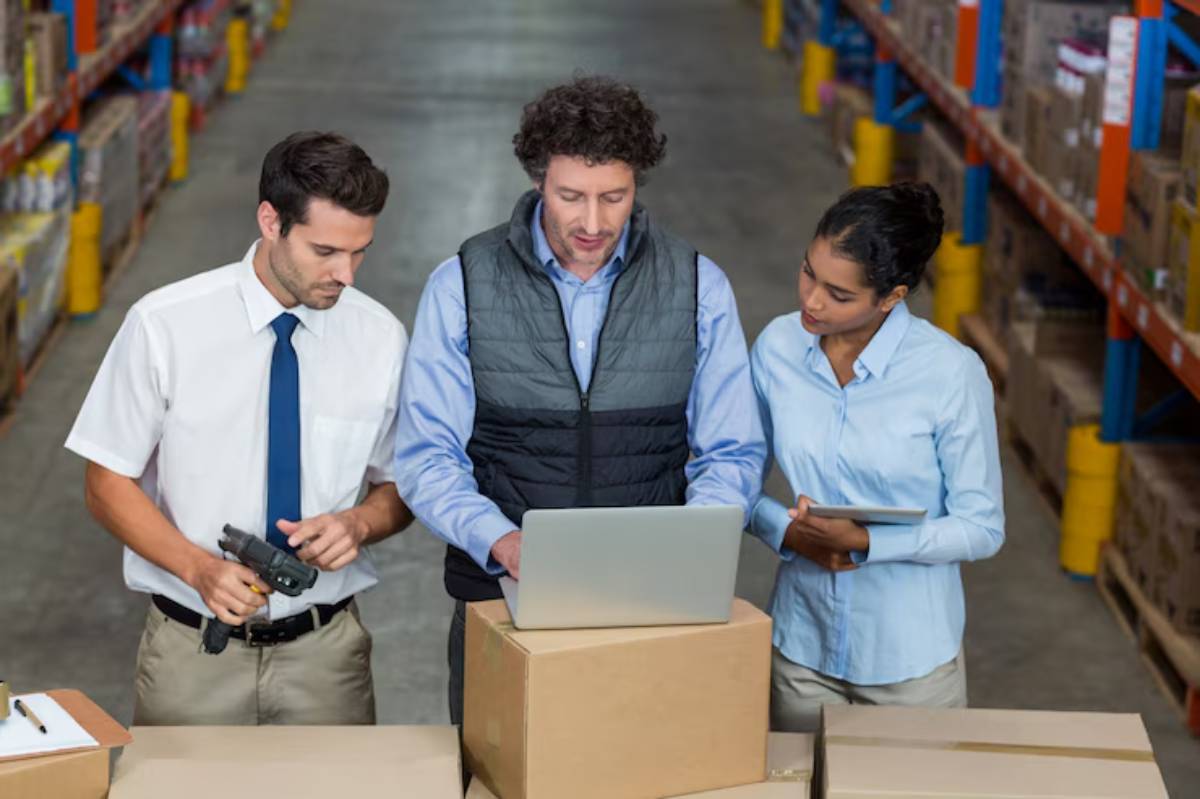
How to Train Staff on Inventory Management Best Practices
Every smooth-running warehouse, retail floor, or e-commerce fulfilment centre relies on a team of trained staff. But without proper training, even the best inventory systems fall short. Miscounts, misplaced stock, and manual errors don’t just disrupt workflow—they drain profit and erode customer trust.
This guide will show you how to effectively deliver inventory training, empowering your team with the skills and systems needed to follow inventory management best practices every day. This expert roadmap will help you onboard new employees and improve processes. You’ll build a smarter and more reliable workforce.
Understanding the Core: Why Inventory Training Matters
Inventory management is more than counting boxes. It’s about ensuring the right products are in the right place at the right time. And while systems and software can support this, your staff are the first line of defence against.
- Stock shrinkage.
- Over-ordering
- Incorrect fulfilment
- Costly inventory errors
Training your team on inventory best practices ensures consistency, accountability, and efficiency.
- Accurate records
- Faster stock takes
- Safer handling
- Better use of technology
The Chartered Institute of Procurement & Supply says that untrained staff are a top cause of inventory inaccuracy for SMEs in the UK.
Quick-Reference Checklist: Staff Training for Inventory Best Practices
Here’s a quick summary to guide your training plan:
- Assess training needs and knowledge gaps
- Define key inventory procedures and standards
- Choose a blend of training methods (visual, hands-on, digital)
- Use real-life examples and role-specific scenarios
- Train on technology tools and software
- Teach error detection and correction protocols
- Document SOPs and distribute them widely
- Use checklists and job aids during daily tasks
- Conduct follow-ups and refresher training regularly
- Monitor KPIs and adjust training accordingly
Step-by-Step Guide: How to Train Staff on Inventory Best Practices
1. Conduct a Training Needs Assessment
Start by identifying:
- Roles with the most inventory interaction
- Staff experience levels
- Recurring issues (e.g. frequent stock discrepancies)
Interview supervisors or review past error logs to pinpoint gaps.
2. Define Clear Inventory Procedures
Document workflows for:
- packing
- Receiving and storing stock
- Replenishment
- Cycle counting and auditing
- Handling damaged or returned items
Keep processes concise, visual, and easy to reference.
3. Use a Blended Training Approach
Combine various learning styles:
- Hands-on walkthroughs in the warehouse
- Video tutorials for software use
- Printed SOPs with photos
- Peer-to-peer shadowing
This ensures better retention and adaptability across learning preferences.
4. Make It Role-Specific
Tailor training to the actual job:
- Warehouse staff focus on scanning, storage zones, and damage checks
- Supervisors learn about stock accuracy, KPI monitoring, and vendor interactions
- Admin teams are trained on system updates and stock reconciliation
Pro Tip: Role-based training reduces cognitive overload and speeds up adoption.
5. Train on Inventory Technology
Don’t assume digital tools are intuitive. Cover:
- Scanning barcodes or RFID
- Logging in and dashboard navigation
- Updating stock levels and entering new SKUs
- Running stock reports and error logs
Use sandbox environments for low-pressure practice.
6. Highlight Common Errors and How to Fix Them
Teach staff how to:
- Spot mismatches in physical vs system stock
- Identify expired or misplaced items
- Correct inaccurate entries or mislabelling
- Follow escalation steps if unsure
Create “what-if” scenarios to test their problem-solving under pressure.
7. Create and Share SOPs
Write clear Standard Operating Procedures for each task and display them:
- In breakrooms
- Near the packing stations
- Within digital systems (as pop-up reminders)
Reinforcement drives consistency.
8. Use Checklists for Daily Tasks
Checklists make habits stick and reduce forgetfulness. Examples:
- End-of-day bin counts
- Weekly replenishment reviews
- Monthly cycle count tasks
Encourage staff to sign off on completed steps for accountability.
9. Follow Up with Refreshers
Plan quarterly micro-trainings or tool-specific updates. Conduct retraining when:
- New systems are introduced
- Processes are changed
- Staff performance metrics drop
10. Track Progress with KPIs
Monitor:
- Stock accuracy rate
- Inventory turnover
- Picking error rate
- Time per cycle count
- Audit pass/fail trends
Use this data to tailor future training and reward improvement.
Secret Tip: Pair new hires with experienced team members. This “buddy system” saves money and boosts hands-on learning.
Best Practices & Additional Insights
- Get feedback: After each session, ask trainees what worked and what didn’t. Training needs continuous improvement, too.
- Make learning fun: Use point systems or competitions for correct counts and safe handling.
- Keep the training dynamic: Update materials regularly to reflect procedural or tech changes.
- Create a knowledge base: A shared Google Drive, Notion board or internal wiki helps staff find answers fast.
Want to level up your operations further? Check out our guide on how to set up an efficient inventory system or reduce inventory holding costs for long-term savings.
Important: Skipping hands-on practice. Verbal instructions alone don’t stick, especially in fast-paced inventory environments.
Real Insight: “Our staff turnover dropped by 20% once we invested in structured, role-specific training. It gave people confidence in their day-to-day.” – Warehouse Manager, Midlands
Frequently Asked Questions (FAQs) for Staff Training on Inventory Management Practices
How often should I retrain staff on inventory management?
Quarterly is ideal. At minimum, plan refreshers every six months or whenever systems and processes change.
What’s the best way to train remote or hybrid staff?
Use video walkthroughs, interactive guides, and LMS platforms. Combine this with occasional in-person workshops, if possible.
Should temporary or seasonal workers be trained the same way?
Yes—at least on core practices like receiving, scanning, and damage control. Streamline training for their roles, but never skip it.
What tools help with training delivery?
Try platforms like Loom (video), Notion (documentation), Google Forms (quizzes), and LearnUpon (LMS). Choose tools that your team finds easy to use.
Conclusion: Empower Your Team, Strengthen Your Inventory
Training your staff on inventory best practices isn’t just about compliance—it’s about efficiency, confidence, and long-term success. Using the right strategy, tools, and delivery helps you cut errors. It also boosts stock accuracy and empowers your team.
Ready to build a training plan that sticks? Download our free Inventory Training Template Pack and get started today. For more operational tips, explore our full inventory systems library.