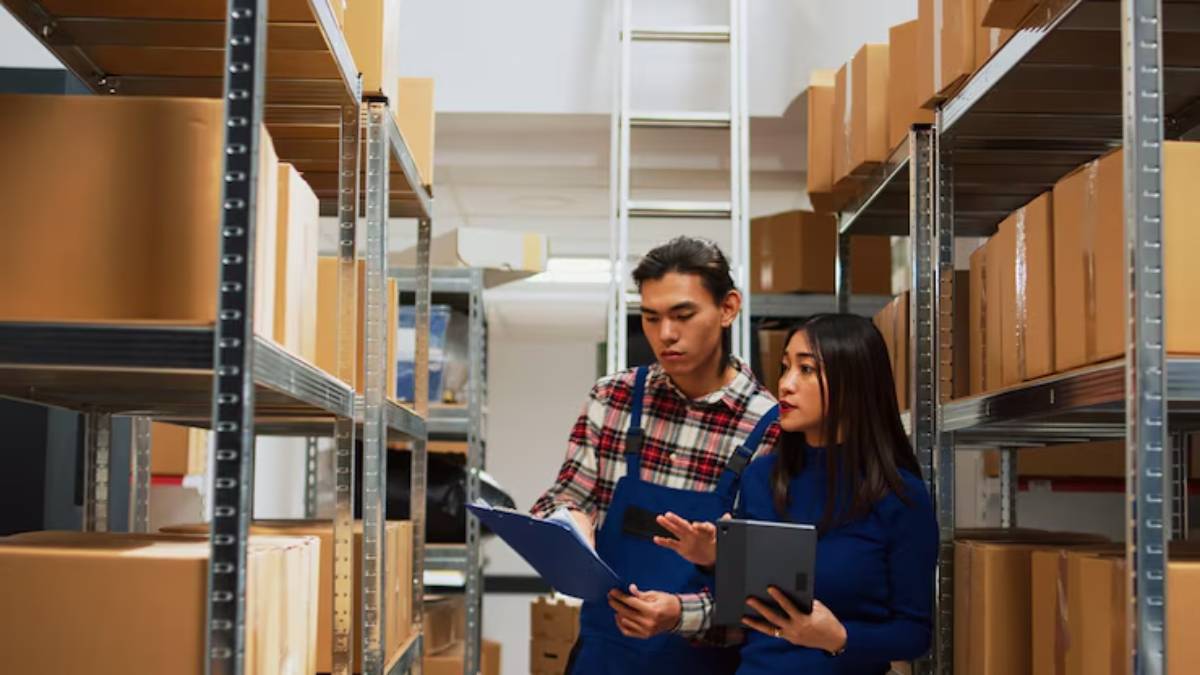
Best Practices for Warehouse Inventory Management
Why Warehouse Inventory Management Matters
Tired of disorganised inventory, misplaced orders, and expensive order mistakes? If you manage a warehouse or supply chain, these problems may feel all too familiar. Managing warehouse inventory goes beyond counting boxes. It is the heart of a smooth logistics system. Managing your warehouse inventory is key, whether you run a small shop or want to grow. It can save you time, cut down stress, and help you save money.
In this article, we’ll see the most useful and actionable warehouse inventory management best practices. You’ll discover smart storage ideas, useful system pairings, important metrics to track, and strategies from successful businesses. By the end, you’ll know how to handle the basics and be ready to optimise event inventory.
So, roll up your sleeves—let’s explore the best ways to optimise your warehouse or your client’s warehouse and keep your business strong.
What Is Warehouse Inventory Management?
Warehouse inventory management means organising, tracking, and controlling goods in a storage facility. It’s the system that ensures the right product is in the right place, at the right time, and in the right quantity.
Effective warehouse management involves:
- Receiving inventory accurately and efficiently
- Storing products to maximise space and accessibility
- Tracking stock levels in real time
- Replenishing inventory before stockouts occur
- Shipping orders quickly and accurately
Without a solid system in place, even small errors can snowball, leading to missed orders, customer complaints, and revenue loss.
Key Principles of Efficient Warehouse Inventory Management
1. Organise for Visibility and Accessibility
One of the simplest yet most impactful steps is creating an organised layout. Poor stockroom organisation leads to delays, misplaced goods, and inefficiency.
Tips:
- Implement a bin location system to assign specific spots for items.
- Group products by category, SKU, or sales volume.
- Use vertical space with shelving units or mezzanine floors.
- Keep fast-moving products near packing/shipping areas.
2. Embrace the FIFO/LIFO Methodology
Inventory methods such as FIFO (First In, First Out) and LIFO (Last In, First Out) affect product freshness and accounting.
- Use FIFO for perishable items or expiration-sensitive goods.
- Use LIFO in certain accounting scenarios or when older stock has less value.
Learn more about implementing FIFO and LIFO effectively here Implementing FIFO and LIFO Methods.
3. Label Everything Clearly
From pallets to individual bins, clear labelling reduces picking errors and speeds up processes.
- Use barcodes or QR codes for scanning.
- Include product name, SKU, and location code.
- Invest in durable, legible label printers.
4. Implement a Robust Inventory System
Manual systems have their place, but they can’t scale. A centralised warehouse management system (WMS) automates tracking, alerts, and reports.
Features to look for in a WMS.
- Real-time inventory tracking
- Barcode/RFID support
- Integration with e-commerce platforms
- Automated reorder points
Technology That Powers Smart Warehouse Management
Technology is no longer optional—it’s essential for efficiency.
1. Inventory Management Software (IMS)
Modern IMS solutions simplify your warehouse tasks. They help you track incoming stock and manage returns.
Popular tools include:
- Zoho Inventory – Great for small to medium businesses
- NetSuite – Offers robust ERP features
- TradeGecko (QuickBooks Commerce) – Ideal for ecommerce sellers
2. Barcode & QR Code Scanning
These technologies eliminate human error and improve speed in stock movement.
- Use handheld scanners or mobile apps
- Scan on receiving, shelving, picking, and dispatch
- Link to IMS or WMS for real-time updates
3. Mobile Inventory Apps
Equip staff with mobile access to the system. Mobile apps help team members update inventory, find items, and check order statuses quickly.
Warehouse Layout and Organisation Tips
An efficient warehouse starts with a smart layout. Aim to minimise movement and maximise productivity.
1. Zoning Your Warehouse
Divide your space into clear zones.
- Receiving – Dedicated area for checking incoming stock
- Storage – Shelves, bins, or racks by product category
- Packing – Tables, materials, and a staging area for dispatch
- Returns – Separate to avoid mixing with salable goods
2. Apply the 80/20 Rule (Pareto Principle)
Focus on the top 20% of products that generate 80% of your movement. These items should be:
- Placed near the packing areas
- Stored at waist level to reduce bending/lifting
3. Use Visual Cues and Signage
Help your team find things fast.
- Colour-coded bins for categories
- Floor markings for zone boundaries
- Digital signage for real-time updates
Best Practices for Inventory Accuracy
1. Regular Cycle Counting
Instead of full annual stocktakes, do frequent cycle counts:
- Count a subset of inventory daily/weekly
- Use ABC analysis to prioritise high-value items
- Match physical counts to system records
This method is less disruptive and helps catch errors early.
2. Schedule Inventory Audits
Periodic audits identify discrepancies between your records and reality.
- Perform quarterly or biannual audits
- Involve a third party for impartiality
- Combine with cycle counting for holistic checks
3. Reconcile Discrepancies Promptly
When mismatches arise:
- Investigate root causes (e.g., theft, mislabelling, returns)
- Update system records
- Adjust processes to prevent recurrence
More tips on reconciliation here Reconciling Inventory Discrepancies.
Metrics That Matter: Tracking Performance
1. Inventory Turnover Ratio
This shows how often you sell and replace stock.
Formula: Cost of Goods Sold / Average Inventory
A high turnover means strong sales, but too high may signal stockouts.
2. Gross Margin Return on Inventory Investment (GMROI)
This metric tells you how much profit you earn for each pound spent on inventory.
Formula: Gross Margin / Average Inventory Cost
3. Days Sales of Inventory (DSI)
Indicates how many days it takes to sell inventory.
Formula: (Average Inventory / Cost of Sales) x 365
Use these metrics to spot trends, eliminate slow movers, and balance inventory levels.
Staff Training and Workflow Management
Even with top-tier software, your warehouse runs on human effort.
1. Train Staff on Inventory Protocols
Provide clear SOPs (Standard Operating Procedures) for:
- Receiving goods
- Labelling and shelving
- Picking and packing
- Returns processing
Use workshops, checklists, and hands-on demos.
2. Use KPIs for Staff Productivity
Track:
- Pick rate per hour
- Error rate per shipment
- Inventory accuracy per team
Reward top performers and offer support where needed.
3. Safety First
Ensure all staff are trained on:
- Lifting techniques
- Equipment use (e.g., forklifts)
- Emergency procedures
Handling Returns and Damaged Goods
Returns can wreak havoc on inventory if not properly managed.
Best Practices:
- Have a separate returns processing area
- Inspect and restock returnable items quickly
- Log damaged goods and write them off properly
- Use barcodes or RFID to track return origins
Real-Life Case Study: A Small Retailer’s Success Story
Take “LuxeHome Decor,” a UK-based small business selling home accessories online. At first, the company used spreadsheets and handwritten notes. This led to misplaced orders, late shipments, and customer complaints.
After LuxeHome set up a WMS and revamped their stockroom with color-coded bins and a mobile barcode system, they noticed:
- 25% faster order processing
- 40% drop in picking errors
- 15% improvement in customer satisfaction reviews
It’s proof that even small steps toward better inventory management can yield big results.
Conclusion: Put Best Practices into Action
Warehouse inventory management doesn’t have to be overwhelming. Use best practices to make your warehouse efficient. Organise clearly, conduct regular audits, and use smart tech.
These methods can save you money, improve accuracy, and keep customers happy. They work well for beginners and those wanting to upgrade their systems.
So, what’s your next move? Start by evaluating your current layout, picking one area to improve, and taking action today.
Want more insights? Explore our guides and practical tips on warehouse and inventory systems. Or leave a comment below—what’s your biggest warehouse challenge right now?