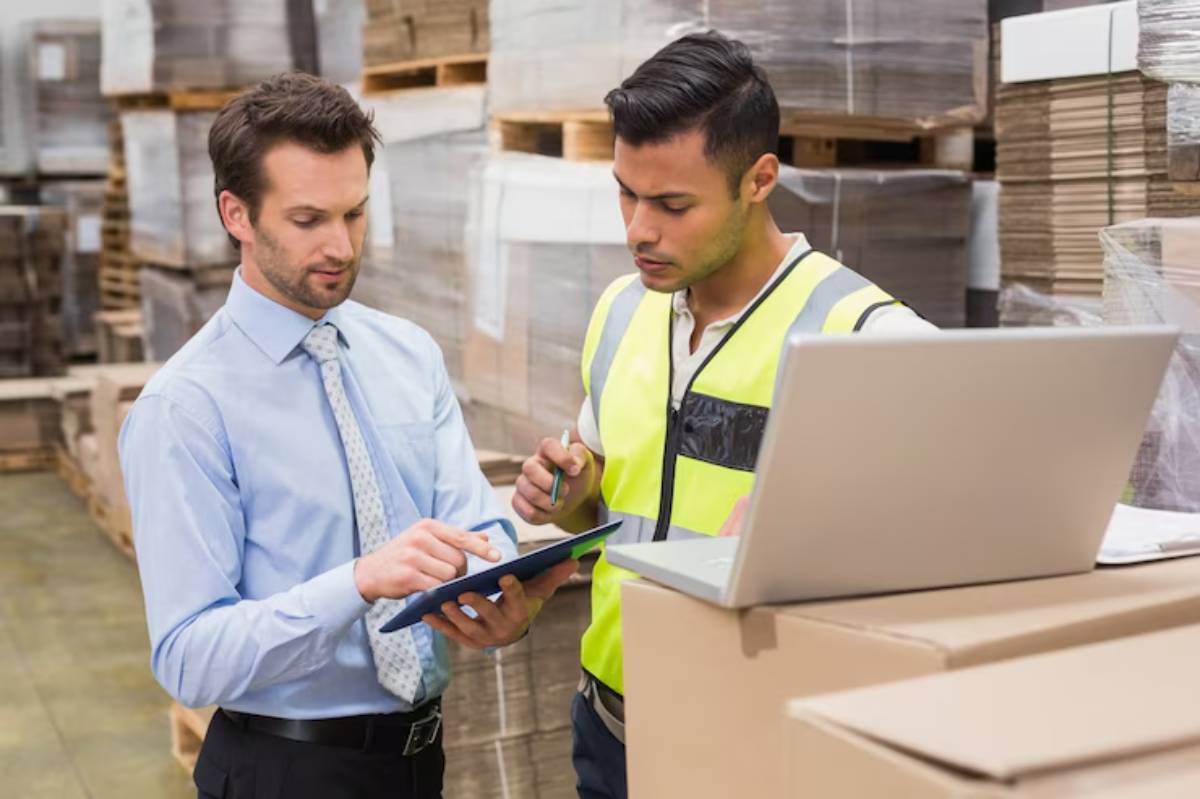
Reconciling Inventory Discrepancies: Mastering Stock Reconciliation and Inventory Control
Turning Inventory Discrepancies Into Operational Wins
Ever felt the sting of confusion when your system shows 200 units in stock, but the shelf holds only 178? Those missing 22 units aren’t just numbers—they’re missed sales, frustrated customers, and money down the drain. Welcome to the tricky world of inventory discrepancies.
Whether you’re running a brick-and-mortar shop or managing an online fulfilment centre, mismatches between recorded and actual inventory can wreak havoc on your business. Thankfully, through stock reconciliation and strong inventory control, you can resolve these issues quickly and build a more reliable system moving forward.
In this comprehensive guide, we’ll explore what causes inventory discrepancies, how to investigate and reconcile them effectively, and best practices to prevent them in the future. By the end, you’ll have the confidence and practical tools to turn inventory headaches into operational strengths.
What Are Inventory Discrepancies?
Defining the Problem
An inventory discrepancy occurs when there’s a mismatch between the stock count in your system and the actual number of items in storage. This gap can show up as.
- Overages: System shows fewer items than are physically present
- Shortages: System shows more items than you actually have
Both types signal a breakdown in your inventory process.
Why They Matter
Ignoring discrepancies means.
- Stockouts or overstocking
- Customer dissatisfaction
- Inaccurate financial reports
- Disrupted demand forecasting
And in the worst cases, it could hint at internal theft or systematic failure.
Common Causes of Inventory Discrepancies
Let’s get to the root of the issue. Here are the most frequent culprits:
1. Human Error
- Mistakes during data entry
- Miscounts during stocktaking
- Mislabelled SKUs
2. Theft and Shrinkage
- Employee theft
- Shoplifting (for retail)
- Unrecorded damages
3. Receiving Errors
- Items received but not recorded
- Wrong quantities marked during delivery
4. Picking and Packing Mistakes
- Wrong item pulled from the shelf
- Double shipment or over-fulfilment
5. Returns Mismanagement
- Returned items not restocked
- Damaged returns mixed with sellable stock
6. System or Integration Glitches
- API sync failures between eCommerce and IMS
- Poorly configured automated reordering systems
The Stock Reconciliation Process Explained
Stock reconciliation is your opportunity to investigate and resolve inventory mismatches.
1: Conduct a Physical Count
Perform a manual stocktake to confirm actual quantities on hand.
- Use barcode scanners or inventory count sheets
- Include all types of stock—new, returned, damaged
- Keep distractions to a minimum to reduce counting errors
If you’re new to audits, see: How to Conduct a Physical Inventory Count.
2: Compare Records Against Count
Generate a system inventory report and compare it line-by-line to your physical count.
- Items with overages
- Items with shortages
- Items completely missing
3: Investigate the Discrepancy
This is the detective work.
- Were items miscounted or mislabelled?
- Was there a picking, packing, or return error?
- Any recent theft or damage?
- Were shipments received and not recorded?
Cross-check with:
- Purchase orders
- Sales invoices
- Delivery notes
- Return slips
4: Update Inventory System
Once verified, adjust stock levels in your inventory management system (IMS). Be sure to:
- Document the reason for the adjustment
- Add internal notes for future audits
- Notify finance if changes affect COGS or valuations
5: Report and Analyse
Create a reconciliation report including:
- Discrepancies found
- Root causes
- Corrective actions
- Recommendations for process improvement
Share this report with key stakeholders to increase transparency and accountability.
Best Practices to Prevent Future Discrepancies
1. Use Barcode or QR Code Systems
Barcode scanning reduces manual data entry errors and makes real-time updates possible.
2. Implement Regular Cycle Counts
Don’t wait for year-end audits. Count different categories weekly or monthly to spot issues early.
See how in Conducting Regular Inventory Audits.
3. Train Staff Thoroughly
Even small mistakes compound quickly. Train employees to:
- Follow SOPs
- Label accurately
- Handle returns correctly
- Use inventory tools properly
4. Use an Integrated Inventory Management System
Your IMS should sync with:
- E-commerce platforms
- Point-of-sale (POS) systems
- Shipping software
This integration reduces duplication and real-time sync issues.
Popular systems include:
- Zoho Inventory
- Cin7
- TradeGecko
5. Secure Your Inventory
Improve loss prevention with:
- CCTV cameras
- Lockable storage for high-value items
- Access logs for stockrooms
6. Document Everything
Maintain logs for:
- Adjustments
- Damages
- Theft incidents
- Vendor disputes
This data provides valuable insight during investigations.
Real-World Example: A Small Retailer’s Reconciliation Win
“Lumi Naturals,” a boutique skincare brand, struggled with monthly stock differences. Their paper-based records and manual updates caused:
- 10% error rates on restocks
- Multiple out-of-stock notifications
- Frustrated repeat customers
Here’s how they fixed it:
- Switched to barcode tracking with Zoho Inventory
- Trained all staff on scanning returns
- Introduced weekly cycle counts on bestsellers
Results:
- Stock accuracy jumped to 97%
- Reduced customer complaints by 60%
- Saved 5 hours/week in admin time
Tools and Templates for Stock Reconciliation
Equip your team with the right tools:
Inventory Reconciliation Template (Excel or Google Sheets)
Fields should include:
- SKU
- Product name
- System quantity
- Counted quantity
- Difference
- Reason for discrepancy
- Adjustment action taken
Barcode Scanners
Recommended for speed and accuracy.
- Honeywell Voyager
- Zebra DS2200
IMS Reporting Dashboard
Choose a system that offers:
- Discrepancy alerts
- Historical adjustments
- Stock movement logs
Tips for Auditing and Reconciling Efficiently
- Start with A-items (high value, high movement)
- Count when the warehouse is quiet
- Double-check unusual variances
- Use two-person teams for critical counts
- Label shelves clearly to avoid misplacement
When to Escalate Inventory Issues
Some discrepancies aren’t just simple errors—they indicate deeper problems.
Escalate if you notice:
- Repeated issues with the same SKUs
- Consistent shrinkage over 3–5%
- Employee patterns (e.g., always on shift during losses)
- System glitches with recurring sync failures
Engage:
- Operations managers
- HR or compliance teams
- Your inventory software support team
Conclusion: Stay Ahead of Discrepancies, Stay Ahead of the Game
Inventory discrepancies are frustrating, yes—but they’re also fixable. And by treating them as signals rather than simply problems, you gain insights that sharpen your entire operation.
Through careful reconciliation, robust tools, regular audits, and well-trained staff, you can reduce discrepancies, improve stock accuracy, and regain confidence in your numbers.
Your next step? Run a quick reconciliation on your top 5 SKUs this week. Start small, learn fast, and build from there.
Got a reconciliation success story or a nagging inventory challenge? Drop a comment below—let’s learn from each other.