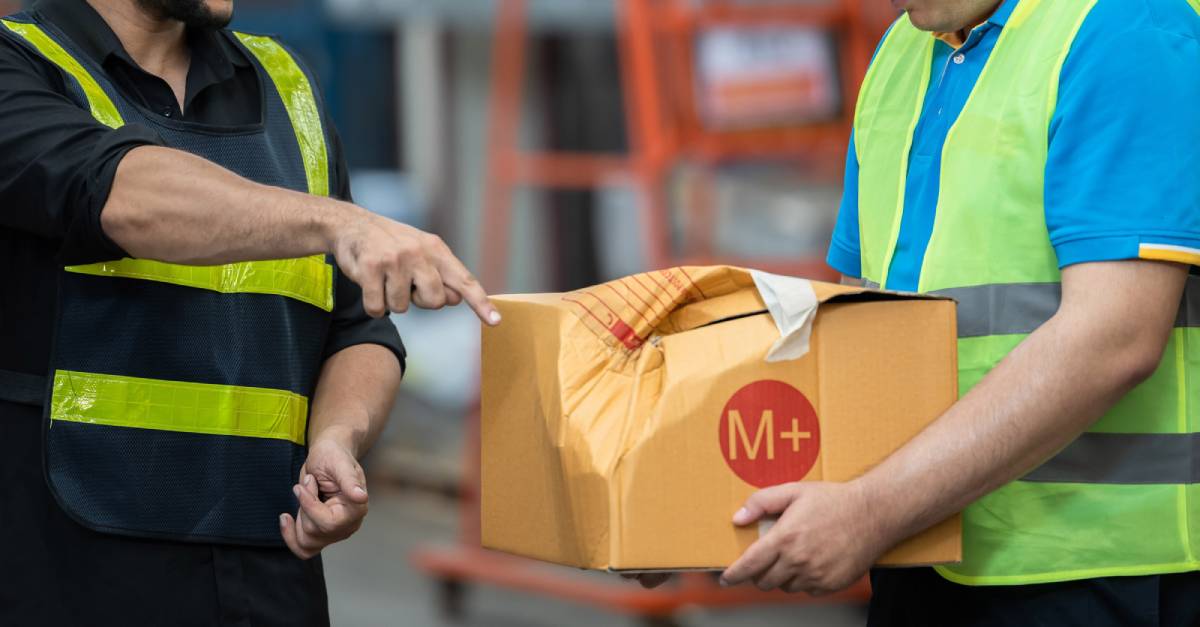
Preventing and Detecting Inventory Shrinkage: The Ultimate Guide to Loss Prevention and Inventory Security
Tackling the Hidden Costs of Inventory Shrinkage
You’ve probably been there — your reports say you should have 500 units of a product, but you only count 480. Those missing 20 units might look small, but they add up. Across all your SKUs, that can lead to a big financial leak. That’s inventory shrinkage, and if left unchecked, it can silently drain your profits.
This article helps you understand inventory shrinkage. It also shows you how to detect, prevent, and control it. You’ll learn:
- How to identify shrinkage early
- Proven loss prevention tactics
- How to secure your inventory from theft, damage, and errors
- Best practices backed by real-world examples and data
If you’re a small seller, warehouse manager, or e-commerce operator, this is your guide. It will help you boost inventory security and cut losses.
What Is Inventory Shrinkage?
Inventory shrinkage is the loss of stock that happens between buying from a supplier and selling to a customer. It’s the gap between your inventory records and what you actually have.
Common Types of Shrinkage
- Theft (employee or external)
- Administrative errors
- Supplier fraud or miscounts
- Shipping errors and damage
- Unrecorded returns or write-offs
Why It Matters
- Cuts into profit margins
- Leads to inaccurate stock levels
- Causes stockouts or overstocking
- Damages customer trust due to fulfilment issues
Root Causes of Inventory Shrinkage
Let’s dig deeper into the triggers of shrinkage so you can recognise them early.
1. Internal Theft
Unfortunately, employee theft is one of the most common causes.
- Pocketing products
- Falsifying records
- Skimming during receiving or returns
2. External Theft
- Shoplifting in retail
- Break-ins at warehouses
- Courier fraud or theft during delivery
3. Human Error
- Miscounts during inventory updates
- Incorrect data entry
- Failure to record damaged or returned goods
4. Vendor Fraud
- Invoicing for items never delivered
- Under-supplying and overcharging
5. Poor Inventory Controls
- No surveillance or tracking system
- Lack of regular audits
- Inconsistent inventory methods
How to Detect Inventory Shrinkage Early
Conduct Regular Stock Reconciliations
Regular inventory audits and reconciliations can help you spot shrinkage patterns early. Use cycle counts or full physical counts to verify accuracy.
Want a methodical process? See Reconciling Inventory Discrepancies.
Monitor Inventory KPIs
Track key performance indicators such as:
- Inventory shrinkage rate = (Cost of shrinkage / Total inventory value) × 100
- Inventory accuracy rate
- Shrinkage trends by SKU or location
Use Technology for Real-Time Tracking
- Barcode or QR code systems
- Cloud-based IMS with alerts for unusual activity
- Automated reconciliation reports
Analyse Historical Patterns
Look for:
- Repeated issues with specific products
- Losses associated with certain staff shifts
- Discrepancies around seasonal spikes
Preventing Inventory Shrinkage: 10 Proven Strategies
1. Install Surveillance Systems
CCTV cameras can:
- Deter theft
- Help investigate incidents
- Provide visual accountability
Place cameras in:
- Receiving and dispatch areas
- Stockrooms
- Loading docks
2. Restrict Access
Not everyone needs access to every area. Apply role-based access to:
- Warehouses
- POS systems
- Returns and receiving stations
3. Use Inventory Management Software
Adopt tools with:
- Real-time tracking
- User activity logs
- Reorder alerts
Popular software:
- NetSuite
- Fishbowl
- Zoho Inventory
4. Conduct Background Checks
Prevention starts at hiring. Run background checks and validate references for staff handling high-value inventory.
5. Implement a Returns SOP
Returned items can easily go missing. Build a clear process to.
- Record each return
- Check condition
- Restock or dispose of accurately
6. Train Your Staff
Employees are your first line of defence. Training should cover.
- Recognising theft or fraud
- Correct stock handling
- Using inventory tools properly
7. Run Random Spot Checks
Surprise counts help:
- Catch discrepancies early
- Keep staff accountable
- Deter misreporting
8. Create a Culture of Integrity
Offer:
- Anonymous reporting options
- Rewards for ethical behaviour
- Clear consequences for theft
9. Secure High-Risk Items
Use locked cages, RFID tags, or additional verification steps for:
- Electronics
- Jewellery
- High-value SKUs
10. Audit Vendors
Don’t overlook supplier shrinkage. Periodically:
- Cross-check purchase orders and delivery receipts
- Randomly verify received quantities
Real-World Example: How Shrinkage Was Caught and Fixed
Harlow Fashion Ltd, a mid-sized online clothing retailer, saw its autumn collection stock shrinking consistently. After three quarterly audits, they realised over £7,000 worth of jackets had mysteriously vanished.
Their Fix:
- Installed CCTV in the receiving
- Switched to barcode tracking
- Segregated access to high-demand SKUs
- Retrained staff on handling returns
Outcome:
- Shrinkage rate dropped from 4.3% to 0.8% in 6 months
- Fulfilment accuracy improved by 22%
Calculating and Benchmarking Inventory Shrinkage
How to Calculate Shrinkage
- Conduct a physical inventory count
- Compare to your recorded stock
- Multiply lost units by unit cost
Shrinkage Formula:
(Recorded Inventory – Actual Inventory) / Recorded Inventory × 100
Acceptable Shrinkage Rate
Retail industry average = 1.4% of total sales (per NRF report)
Keep your shrinkage rate below 1% if possible.
Inventory Security Checklist
Warehouse Security
- CCTV installed and operational
- Secure entry points with log access
- Alarm system on off-hours
Employee Controls
- Defined roles and permissions
- Staff rotation in high-risk areas
- Regular ethical training
Technology Tools
- Real-time IMS
- Barcode/RFID system
- Audit trail for all stock movements
Operations Best Practices
- Clear SOPs for receiving and returns
- Documented stock adjustment logs
- Regular audits and surprise checks
Inventory Shrinkage vs. Inventory Errors
It’s important to distinguish between:
- Shrinkage = actual loss (stolen, damaged, missing)
- Errors = data or process mistakes (e.g., mislabelling, wrong SKU entry)
Both cause inaccuracies, but require different fixes:
- Shrinkage = focus on prevention and security
- Errors = focus on process, training, and software
Explore solutions in Using Cycle Counting for Inventory Accuracy.
Conclusion: Secure Your Stock, Secure Your Success
Shrinkage isn’t just a retail nuisance — it’s a hidden cost that chips away at your bottom line. But with the right combination of inventory control, loss prevention strategies, and employee training, you can take back control and build a secure, resilient inventory system.
Start today by auditing your top 10 high-value SKUs. Implement just one of the prevention tactics discussed, and you’ll already be one step ahead.
Have a shrinkage horror story or prevention tip to share? Drop it in the comments — your experience could help someone else prevent loss too.