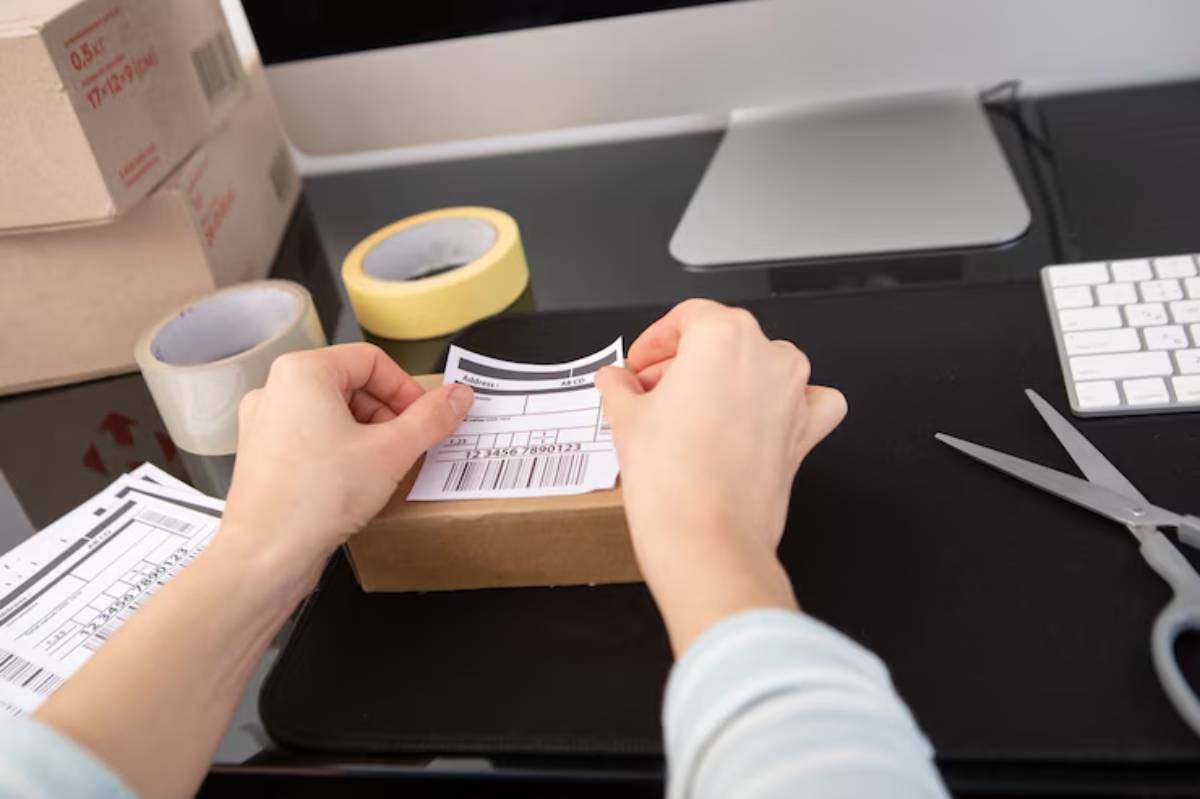
Labelling and Categorising Inventory Effectively: A Complete Guide to Smart Inventory Organisation
Why Labelling and Categorisation Matter More Than You Think
Ever spent half an hour searching for a product that should have been right there on the shelf? Or sent out the wrong item to a customer because two similar-looking boxes weren’t clearly labelled? If so, you’re not alone. Bad inventory organisation can make even the best-stocked warehouse a logistical mess.
Labelling and categorising inventory effectively isn’t just about being neat. It’s about being efficient, accurate, and ready to scale. How you label and categorise your stock matters. It affects order accuracy, cycle counts, restocking, and customer satisfaction. This is true for both small ecommerce stores and growing suppliers.
This article will guide you on the best ways to label and organise your inventory. You’ll learn about useful tools and real-life tactics to do it like a pro. We’ll talk about naming conventions, categorisation strategies, barcodes, colour-coding, and storage integration.
By the end, you’ll not only understand why inventory labelling matters—you’ll have a practical blueprint to improve your own stock system.
The Foundations of Inventory Labelling and Categorisation
What Is Inventory Labelling?
Inventory labelling means giving identifiers, such as barcodes, SKUs, or alphanumeric codes, to each item, bin, or pallet in your warehouse or stockroom.
- Track inventory movement
- Prevent mix-ups
- Speed up stock checks
- Simplify restocking
What Is Inventory Categorisation?
Categorisation means grouping inventory based on common attributes such as:
- Product type
- Brand
- Usage frequency
- Seasonality
- Size or weight
Clear labelling helps categorise stock, making it easier and faster to find and manage.
Key Benefits of Organised Labelling and Categorisation
Here’s what an effective organisation can do for your business:
- Reduce picking errors
- Speed up order fulfilment
- Improve inventory accuracy
- Lower shrinkage and loss
- Enhance staff training and workflow
If you’re still operating with sticky notes or vague handwritten codes, it might be time for an upgrade.
How to Label Inventory Effectively
1: Establish Clear Naming Conventions
Start with creating consistent, logical item names or Stock Keeping Units (SKUs).
- Descriptive (e.g. “BLU-Tshirt-L” for a blue large T-shirt)
- Consistent (same format across all products)
- Scalable (can accommodate new items without confusion)
Avoid: Random numbers or overly long codes like “SKU-0923aXLr09-blea#44”.
2: Use Barcodes or QR Codes
Digitising your labelling system allows you to:
- Scan items during picking, receiving, and audits
- Connect with your inventory software
- Reduce manual entry errors
Tools to use:
- Barcode printers (like Zebra or Dymo)
- Mobile scanning apps
- Integrated inventory management software (IMS)
Explore more in our guide to Utilising Barcodes and QR Codes in Inventory Management.
3: Label Everything—Bins, Shelves, and Products
Think beyond product packaging:
- Bin labels identify storage spots
- Shelf tags indicate categories or zones
- Product tags link items to your IMS
Use waterproof labels for durability and bold, readable fonts for clarity.
4: Colour Code for Quick Visual Reference
Colour coding adds a layer of visual guidance, especially useful for high-volume warehouses.
Examples:
- Red labels for high-demand items
- Green bins for returns
- Yellow shelves for perishable stock
Just ensure your team is trained on the colour system.
Smart Categorisation Strategies
Use ABC Analysis for Prioritisation
ABC analysis segments inventory by value and importance.
- A items: High-value, low-quantity (focus attention here)
- B items: Moderate value and demand
- C items: Low-cost, high-volume (automate if possible)
This method helps optimise counting frequency, reordering, and storage location.
Group by Product Type or Function
Depending on your stock variety, you might group items by:
- Category (e.g., electronics, clothing)
- Size (e.g., small, medium, large)
- Sales channel (e.g., Amazon, Shopify)
Categorise by Movement or Velocity
Stock that moves frequently should be:
- Stored near packing zones
- Tagged with fast-pick labels
- Replenished more often
Slow-movers can be stored higher or in less accessible zones.
Tools and Software to Support Labelling & Categorisation
The right tech can take your system from manual to magnificent.
Inventory Management Systems (IMS)
IMS platforms like Cin7, Zoho Inventory, or TradeGecko help:
- Generate and print barcode labels
- Assign categories and SKUs
- Track inventory in real-time
Want to explore options? Check out our post on the Top Inventory Management Software for Small Businesses.
Label Printing Tools
Options include:
- Thermal printers for long-lasting, scannable labels
- Label design software (like BarTender or DYMO)
Ensure labels are legible, durable, and the right size for your packaging.
Creating an Inventory Labelling Policy
Every team needs a clear SOP (Standard Operating Procedure) for labelling.
What to Include:
- Who is responsible for labelling (and when)
- Where labels are applied (on item, box, or shelf)
- What happens when labels fade or go missing
- How to audit and maintain label consistency
Regular training and refreshers keep the system strong.
Integrating Labelling and Categorisation with Warehouse Layout
Labelling and categorisation go hand in hand with physical layout.
Set Up Logical Zones
- Inbound, putaway, pick, and pack
- Assign codes and signs to each zone
- Align bin codes with product types
Use Location-Based Labelling
Give each shelf and bin a unique code, like “A3-02-07”:
- Aisle 3
- Shelf 2
- Bin 7
This system makes it easy for staff to find anything quickly.
Real-Life Example: The Turnaround of a Struggling Stockroom
“UrbanVibe Apparel” is a growing online fashion brand. It faced issues with misplaced items and long picking times. They had no SKU system, and items were stored wherever there was space.
After introducing:
- A standard SKU format
- Coloured bin tags by product category
- Barcode scanners integrated with TradeGecko
They saw:
- 43% reduction in order errors
- 30% faster picking times
- Improved inventory count accuracy by 55%
The change wasn’t expensive, but it was transformative.
Tips for Training Staff on Inventory Organisation
Staff are the glue that keeps your system running. Make sure they’re aligned.
Training Ideas:
- Hands-on labelling exercises
- Quizzes on the SKU meaning
- Shadow sessions with senior staff
- Walkthroughs of categorisation logic
Incentivise precision with friendly competitions or performance-based rewards.
Common Mistakes to Avoid
- Inconsistent label formats – leads to confusion and mispicks
- Faded or damaged labels – check print quality and durability
- Over-categorisation – too many sub-groups can overwhelm rather than help
- Lack of documentation – maintain an updated SOP and training guide
Conclusion: A Small Fix That Delivers Big Results
Effective inventory labelling and categorisation don’t require a warehouse the size of Amazon’s. All you need is a system that fits your business, consistent practices, and a team that knows how to follow them.
When done right, it brings clarity to chaos, speeds up daily tasks, and lays the groundwork for scaling. Labelling and categorisation are essential. It doesn’t matter if you run a stockroom from your garage or manage a fulfilment centre. They help keep operations running smoothly and customers satisfied.
So here’s your next step: Audit your current labelling system, choose one area to improve, and start small—but start now.
Have a success story or question? Leave a comment below, and share your labelling wins or challenges—we’d love to hear from you.